Die statischen Fehlerquellen vonKoordinatenmessgerätDazu gehören hauptsächlich: der Fehler des Koordinatenmessgeräts selbst, wie der Fehler des Führungsmechanismus (gerade Linie, Drehung), die Verformung des Referenzkoordinatensystems, der Fehler der Sonde, der Fehler der Standardgröße;der Fehler, der durch verschiedene Faktoren im Zusammenhang mit den Messbedingungen verursacht wird, wie z. B. den Einfluss der Messumgebung (Temperatur, Staub usw.), den Einfluss der Messmethode und den Einfluss einiger Unsicherheitsfaktoren usw.
Die Fehlerquellen von Koordinatenmessgeräten sind so kompliziert, dass es schwierig ist, sie einzeln zu erkennen, zu trennen und zu korrigieren, und im Allgemeinen nur diejenigen Fehlerquellen, die einen großen Einfluss auf die Genauigkeit von Koordinatenmessgeräten haben, und solche, die einfacher zu beheben sind getrennt sind korrigiert.Der derzeit am meisten erforschte Fehler ist der Mechanismusfehler von Koordinatenmessgeräten.Die meisten in der Produktionspraxis verwendeten KMGs sind KMGs mit orthogonalen Koordinatensystemen. Bei allgemeinen KMGs bezieht sich der Mechanismusfehler hauptsächlich auf den Fehler der linearen Bewegungskomponente, einschließlich Positionierungsfehler, Geradheitsbewegungsfehler, Winkelbewegungsfehler und Rechtwinkligkeitsfehler.
Um die Genauigkeit der zu bewertenKoordinatenmessgerätbzw. zur Durchführung einer Fehlerkorrektur wird das Modell des inhärenten Fehlers des Koordinatenmessgeräts zugrunde gelegt, in dem die Definition, Analyse, Übertragung und der Gesamtfehler jeder Fehlerposition angegeben werden müssen.Der sogenannte Gesamtfehler bezieht sich bei der Genauigkeitsüberprüfung von KMGs auf den kombinierten Fehler, der die Genauigkeitseigenschaften von KMGs widerspiegelt, d. h. die Anzeigegenauigkeit, die Wiederholgenauigkeit usw.: In der Fehlerkorrekturtechnologie von KMGs bezieht er sich auf der Vektorfehler räumlicher Punkte.
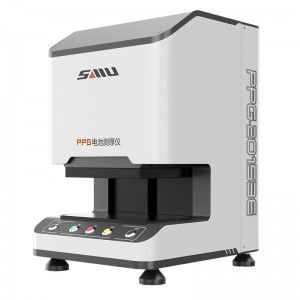
Mechanismusfehleranalyse
Aufgrund der Mechanismuseigenschaften von KMG begrenzt die Führungsschiene fünf Freiheitsgrade für das von ihr geführte Teil, und das Messsystem steuert den sechsten Freiheitsgrad in Bewegungsrichtung, sodass die Position des geführten Teils im Raum durch das bestimmt wird Führungsschiene und dem Messsystem, zu dem sie gehört.
Sondenfehleranalyse
Es gibt zwei Arten von KMG-Messtastern: Kontaktmesstaster werden entsprechend ihrer Struktur in zwei Kategorien unterteilt: Schalten (auch bekannt als Touch-Trigger oder dynamische Signalgebung) und Scannen (auch bekannt als proportionale oder statische Signalgebung).Fehler der Schaltsonde, die durch den Schalthub, die Anisotropie der Sonde, die Streuung des Schalthubs, die Totzone beim Zurücksetzen usw. verursacht werden. Fehler der Abtastsonde, die durch die Kraft-Verschiebungs-Beziehung, die Verschiebung-eine-Verschiebungs-Beziehung, Kreuzkopplungsstörungen usw. verursacht werden.
Der Schalthub des Tasters für den Taster- und Werkstückkontakt mit dem Tasterhaar hört die Tasterauslenkung um eine Strecke.Dies ist der Systemfehler der Sonde.Die Anisotropie der Sonde ist die Inkonsistenz des Schalthubs in alle Richtungen.Es handelt sich um einen systematischen Fehler, der jedoch normalerweise als Zufallsfehler behandelt wird.Die Zerlegung des Schalterwegs bezieht sich auf den Grad der Streuung des Schalterwegs bei wiederholten Messungen.Der tatsächliche Messwert wird als Standardabweichung des Schalterwegs in eine Richtung berechnet.
Das Zurücksetzen des Totbandes bezieht sich auf die Abweichung der Sondenstange von der Gleichgewichtsposition. Wenn Sie die äußere Kraft entfernen, wird die Stange durch die Federkraft zurückgesetzt. Aufgrund der Rolle der Reibung kann die Stange jedoch nicht in die ursprüngliche Position zurückkehren. Dies ist eine Abweichung von der Gleichgewichtsposition Die ursprüngliche Position ist die Rücksetz-Totzone.
Relativer integrierter Fehler des CMM
Der sogenannte relative integrierte Fehler ist die Differenz zwischen dem gemessenen Wert und dem wahren Wert des Punkt-zu-Punkt-Abstands im Messraum des KMG, der durch die folgende Formel ausgedrückt werden kann.
Relativer integrierter Fehler = Entfernungsmesswert und wahrer Entfernungswert
Für die Annahme von KMG-Quoten und die regelmäßige Kalibrierung ist es nicht erforderlich, den Fehler jedes Punktes im Messraum genau zu kennen, sondern nur die Genauigkeit des Koordinatenmesswerkstücks, die anhand des relativen integrierten Fehlers des KMG beurteilt werden kann.
Der relative integrierte Fehler spiegelt nicht direkt die Fehlerquelle und den endgültigen Messfehler wider, sondern spiegelt nur die Größe des Fehlers bei der Messung der auf den Abstand bezogenen Abmessungen wider, und die Messmethode ist relativ einfach.
Raumvektorfehler des KMG
Der Raumvektorfehler bezieht sich auf den Vektorfehler an jedem Punkt im Messraum eines KMG.Es ist die Differenz zwischen einem beliebigen festen Punkt im Messraum in einem idealen rechtwinkligen Koordinatensystem und den entsprechenden dreidimensionalen Koordinaten im tatsächlichen, vom KMG festgelegten Koordinatensystem.
Theoretisch ist der Raumvektorfehler der umfassende Vektorfehler, der durch Vektorsynthese aller Fehler dieses Raumpunkts erhalten wird.
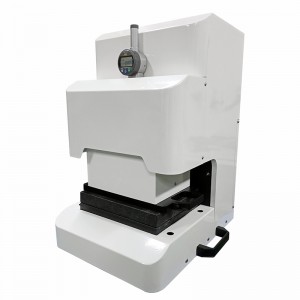
Die Messgenauigkeit von KMG ist sehr anspruchsvoll, und es besteht aus vielen Teilen und einer komplexen Struktur sowie vielen Faktoren, die den Messfehler beeinflussen.Es gibt vier Hauptquellen für statische Fehler bei mehrachsigen Maschinen wie KMGs:
(1) Geometrische Fehler, die durch die begrenzte Genauigkeit von Strukturteilen (z. B. Führungen und Messsystemen) verursacht werden.Diese Fehler werden durch die Fertigungsgenauigkeit dieser Strukturteile und die Justiergenauigkeit bei Installation und Wartung bestimmt.
(2) Fehler im Zusammenhang mit der endlichen Steifigkeit der Mechanismusteile des KMG.Sie werden hauptsächlich durch das Gewicht der beweglichen Teile verursacht.Diese Fehler werden durch die Steifigkeit der Strukturteile, ihr Gewicht und ihre Konfiguration bestimmt.
(3) Thermische Fehler, wie z. B. Ausdehnung und Biegung der Führung, die durch einzelne Temperaturänderungen und Temperaturgradienten verursacht werden.Diese Fehler werden durch die Maschinenstruktur, die Materialeigenschaften und die Temperaturverteilung des KMG bestimmt und durch externe Wärmequellen (z. B. Umgebungstemperatur) und interne Wärmequellen (z. B. Antriebseinheit) beeinflusst.
(4) Sonden- und Zubehörfehler, hauptsächlich einschließlich Änderungen des Radius des Sondenendes, die durch den Austausch der Sonde, das Hinzufügen einer langen Stange oder das Hinzufügen anderen Zubehörs verursacht werden;anisotroper Fehler, wenn die Sonde die Messung in verschiedenen Richtungen und Positionen berührt;der Fehler, der durch die Drehung des Rundschalttisches verursacht wird.
Zeitpunkt der Veröffentlichung: 17. November 2022